Caps Cases boxes clever with expansion fuelled by £1.8m Lloyds deal
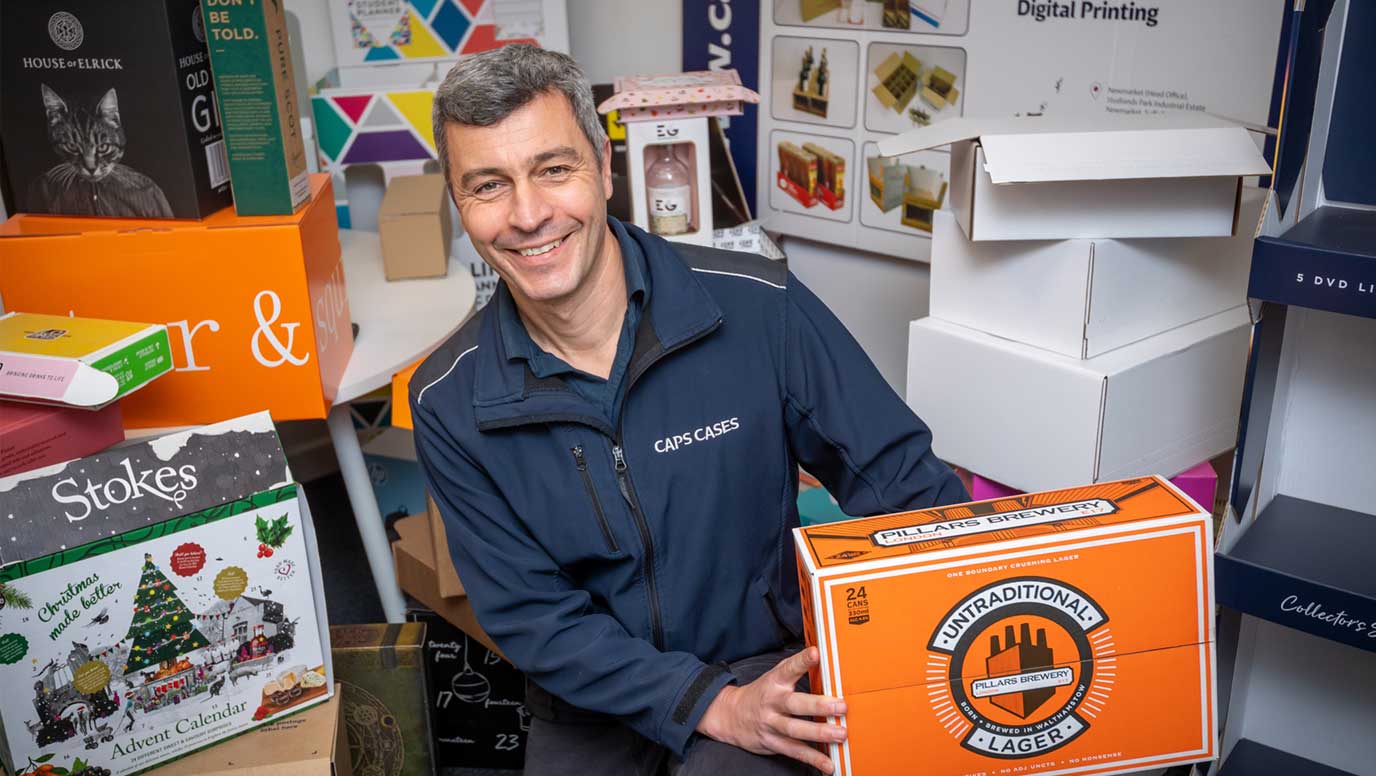
Corrugated cardboard box maker Caps Cases has modernised its production line with advanced machinery supported by a Green Asset Finance Package from Lloyds and the investment has helped the business triple its output from 5,000 boxes to 15,000 per hour.
Caps Cases produced 150 million bespoke printed boxes for brands across the UK last year, predominantly in the retail and FMCG in sectors. Its high-quality graphics are designed to help brands better communicate their messaging through their packaging, which has become more important as more consumers choose to shop online.
Caps Cases is now expecting to shorten its delivery times and boost its capacity to take on more orders. With demand in the e-commerce sector, for example, growing, this will allow Caps Cases to capitalise on the increasing number of organisations looking to improve the quality of packaging for their customers.
The business, which employs 220 people across its sites in Newmarket, Glasgow, Northampton and Peterborough, is now targeting a 10 per cent increase in turnover within the next three years.
This more efficient equipment has already helped to reduce the firm’s carbon emissions by 10 per cent in a drive to be carbon neutral by 2030.
This is the latest round of changes the family-run business has made to prioritise sustainability at its Newmarket hub, along with 1,800 solar panels and a 10-strong electric vehicle fleet to manage its deliveries across the UK, as part of its commitment to ensuring it has a positive environmental impact.
Trevor Bissett, managing director at Caps Cases, said: “The e-commerce boom that we saw following the pandemic has showed no signs of slowing down. That’s why it’s important for us as a business to continue investing in our operations so we’re in a position to support brands with high-quality and well-designed packaging.
“These new machines are at the core of our production processes, day after day, which was why we opted to make this investment in more modern and efficient equipment will serve us and our clients for many years to come. We’re already seeing the benefits from it, boosting our productivity and capacity so we’re able to offer shorter lead-times, and can see this is providing a strong foundation for us to continue to grow with our customers.”